UK Industrial Coatings Guide: Best Solutions & Choices for Industries
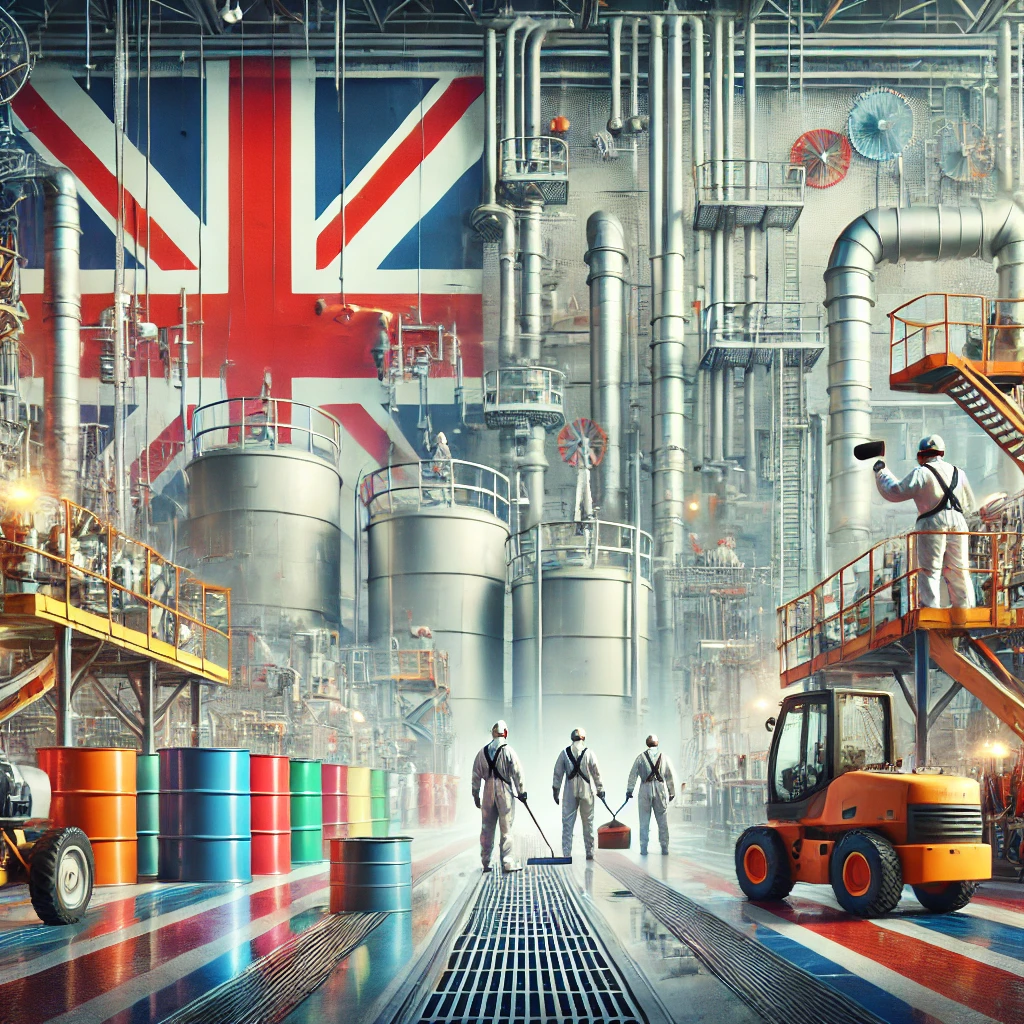
Key Takeaways
- Industrial coatings protect materials from corrosion and enhance their durability, critical for maintaining efficiency in industrial operations.
- Choosing the right coating depends on the environment, exposure conditions, and specific performance requirements.
- Epoxy and polyurethane coatings are popular for their strong protective qualities and versatility in various industries.
- Different industries, like automotive and marine, require specialized coatings to meet their unique challenges.
- Regular maintenance and inspection of coatings can significantly extend the lifespan of industrial equipment.
Introduction to Industrial Coatings in the UK
In the industrial world, coatings are the unsung heroes that keep everything running smoothly. They protect surfaces from corrosion, wear, and environmental damage. In the UK, where industries range from automotive to aerospace, choosing the best industrial coatings is crucial. It’s not just about picking a paint; it’s about selecting a solution that enhances efficiency and longevity.
The Importance of Choosing the Right Coatings
Choosing the right coating is like choosing the right armour for a knight. It needs to withstand the specific battles it will face. In industries, this means considering factors like the type of material being coated, the environmental conditions it will face, and the performance requirements. A coating that excels in a dry, indoor environment might not perform well in a wet, salty marine setting.
Key Benefits of Industrial Coatings
Industrial coatings offer a multitude of benefits that go beyond simple protection. They enhance the efficiency of operations by reducing maintenance needs and extending the lifespan of equipment. Additionally, they improve safety by providing non-slip surfaces and protecting against hazardous chemicals.
Benefit | Description |
---|---|
Protection | Shields surfaces from wear, tear, and environmental damage |
Corrosion Resistance | Prevents rust and corrosion, extending product life and functionality |
Safety Enhancement | Provides non-slip surfaces and improves workplace safety |
Durability | Increases longevity of equipment and structures |
Easy Cleaning | Facilitates easier maintenance and cleaning of surfaces |
Chemical Resistance | Protects against harsh chemicals and cleaning agents |
Aesthetic Improvement | Enhances visual appeal of products and structures |
Abrasion Resistance | Prevents material wear from frequent use or harsh conditions |
Energy Efficiency | Some coatings can improve insulation, leading to energy savings |
Cost Reduction | Reduces maintenance costs and extends asset lifecycles |
Common Applications Across Industries
Industrial coatings are used in a variety of applications across different industries. From protecting the hulls of ships in the marine industry to providing a durable finish for automotive parts, these coatings are integral to maintaining the integrity and functionality of industrial components.
Types of Industrial Coatings
There are several types of industrial coatings, each with its unique properties and applications. Understanding these can help in selecting the best option for your needs. For more detailed information, you can refer to this Industrial Coatings Selection Guide.
Epoxy Coatings
Epoxy coatings are known for their excellent adhesion, chemical resistance, and durability. They are often used in environments where surfaces are exposed to harsh chemicals and heavy wear. For example, in manufacturing plants, epoxy coatings protect floors from spills and heavy machinery.
Polyurethane Coatings
Polyurethane coatings offer a flexible, abrasion-resistant finish that is ideal for surfaces that experience frequent impacts or movements. These coatings are often used in industries where flexibility and durability are paramount, such as in the automotive sector.
- High resistance to UV rays, making them suitable for outdoor applications.
- Excellent gloss and color retention, ensuring aesthetic appeal.
- Fast drying times, reducing downtime during application.
Zinc-Rich Primers
Zinc-rich primers are primarily used for their corrosion resistance properties. They are often applied to steel surfaces to prevent rust and are commonly used in the construction and infrastructure sectors.
- Provide sacrificial protection to steel, extending its life.
- Can be top-coated with various finishes for enhanced protection.
Most importantly, zinc-rich primers are an essential part of a comprehensive coating system, especially in environments prone to corrosion.
Powder Coatings
Powder coatings offer a durable, environmentally friendly option for industrial applications. They are applied as a free-flowing powder and then cured under heat, forming a hard finish that is tougher than conventional paint.
Because they contain no solvents, powder coatings release negligible amounts of volatile organic compounds (VOCs), making them an eco-friendly choice. They are widely used in appliances, automotive parts, and outdoor furniture due to their robust finish and environmental benefits.
Factors to Consider in Coating Selection
Choosing the right industrial coating involves several key considerations that can significantly impact the efficiency and longevity of your operations. It’s not just about picking a color or finish; it’s about understanding the specific needs and conditions of your industry and environment. For more detailed information, you can refer to the Industrial Coatings Selection Guide.
Environment and Exposure Conditions
The environment in which the coating will be used plays a critical role in its selection. For instance, coatings in marine environments must resist saltwater corrosion, while those in industrial plants may need to withstand chemical exposure and high temperatures. Always assess the environmental factors to ensure the coating’s effectiveness and durability. For a deeper understanding, explore industrial architectural coatings and their applications.
Performance and Durability Requirements
Performance expectations and durability requirements should guide your choice of coating. Consider the following: the importance of selecting the right architectural paints to enhance both durability and performance.
- How long do you need the coating to last?
- What types of wear and tear will it endure?
- Does it need to be flexible or rigid?
By understanding these factors, you can select a coating that not only meets but exceeds your performance expectations. For instance, in the automotive industry, coatings must endure constant movement and impact, making polyurethane a popular choice due to its flexibility and resilience.
Regulatory and Compliance Considerations
Regulations and compliance standards are crucial when selecting industrial coatings. In the UK, certain coatings must meet specific environmental and safety standards. Always check local regulations to ensure compliance, especially concerning VOC emissions and hazardous material usage. Non-compliance can result in fines and operational disruptions.
Industry-Specific Coating Solutions
Different industries have unique challenges and requirements, making it essential to choose coatings tailored to those specific needs. Let’s explore some industry-specific solutions.
Coatings for the Automotive Industry
“In the automotive industry, coatings must not only protect but also enhance the vehicle’s appearance. This dual role requires coatings that offer superior protection against weathering while maintaining a high gloss finish.” – Automotive Coatings Expert
Automotive coatings often include a combination of primers, basecoats, and clearcoats to provide comprehensive protection and aesthetic appeal. Epoxy primers are frequently used for their excellent adhesion and corrosion resistance, while polyurethane topcoats offer durability and UV protection.
For instance, a car manufacturer might use an epoxy primer to protect the vehicle’s metal body, followed by a polyurethane topcoat for a glossy, long-lasting finish. This combination ensures the car remains protected and visually appealing for years.
Protective Solutions for the Marine Sector
The marine sector faces unique challenges due to constant exposure to saltwater and harsh weather conditions. Coatings for this industry must offer exceptional corrosion resistance and durability.
Zinc-rich primers are often used as the first line of defense against corrosion, followed by epoxy or polyurethane topcoats for added protection. These coatings help prevent rust and extend the lifespan of marine vessels, reducing maintenance costs and downtime.
Coating Choices for the Aerospace Industry
Aerospace coatings must meet stringent standards for performance and safety. They need to withstand extreme temperatures, pressure changes, and UV exposure while maintaining minimal weight.
High-performance epoxy and polyurethane coatings are commonly used in this industry. They offer excellent adhesion, chemical resistance, and flexibility, crucial for aircraft operating under varying conditions. Besides that, these coatings contribute to fuel efficiency by maintaining a smooth, aerodynamic surface.
Solutions for the Construction Industry
In construction, coatings are vital for protecting infrastructure from environmental damage and wear. They are used on everything from bridges to buildings, providing essential protection against corrosion, UV rays, and chemical exposure.
Epoxy and polyurethane coatings are popular choices due to their durability and versatility. They are applied to steel structures, concrete surfaces, and even wood, ensuring long-term protection and aesthetic appeal. Additionally, these coatings can enhance safety by providing non-slip surfaces in high-traffic areas.
Case Studies of Effective Industrial Coatings
Real-world examples demonstrate the effectiveness of industrial coatings in enhancing efficiency and longevity. Let’s explore a few success stories.
In a manufacturing plant, the application of epoxy floor coatings significantly reduced maintenance costs and downtime. The coating’s resistance to chemical spills and heavy machinery wear ensured a safe and efficient working environment.
Another example comes from the oil and gas industry, where zinc-rich primers and epoxy topcoats protected pipelines from corrosion. This combination extended the pipelines’ lifespan, preventing costly repairs and environmental damage.
Successful Implementation in Manufacturing
In the manufacturing sector, industrial coatings have proven to be a game-changer. One notable example is a large-scale automotive parts manufacturer that faced frequent maintenance shutdowns due to floor damage from heavy machinery and chemical spills. By applying a robust epoxy floor coating, the company significantly reduced maintenance costs and increased operational uptime. The epoxy coating provided excellent resistance to chemical exposure and mechanical wear, creating a safer and more efficient work environment. This strategic move not only improved productivity but also enhanced the facility’s overall safety standards.
Innovative Solutions in Oil and Gas
The oil and gas industry presents unique challenges due to harsh environmental conditions and the presence of corrosive substances. In this sector, innovative coating solutions have played a critical role in maintaining the integrity of pipelines and equipment. A case study from a leading oil company highlights the effectiveness of using zinc-rich primers followed by epoxy topcoats to protect offshore drilling rigs.
These coatings offered exceptional corrosion resistance, even in the aggressive marine environment. As a result, the company witnessed a significant reduction in maintenance costs and extended the lifespan of their equipment. This approach not only safeguarded their assets but also minimized environmental risks associated with oil spills.
Conclusion and Expert Recommendations
Industrial coatings are an essential component in enhancing efficiency and longevity across various industries. From automotive to aerospace, these coatings offer protection, durability, and aesthetic appeal, making them indispensable for maintaining industrial operations. When selecting a coating, it is crucial to consider the specific environmental conditions, performance requirements, and regulatory standards.
For optimal results, I recommend partnering with experienced coating suppliers who can provide tailored solutions based on your industry needs. Regular maintenance and inspections are also vital to ensure the coatings remain effective and continue to protect your assets.
In conclusion, investing in the right industrial coatings can significantly improve your operational efficiency, reduce costs, and extend the lifespan of your equipment. By making informed decisions and leveraging the latest coating technologies, you can ensure your industry remains competitive and resilient in the face of challenges.
Frequently Asked Questions (FAQ)
What are the main differences between epoxy and polyurethane coatings?
Epoxy coatings are known for their excellent adhesion, chemical resistance, and durability, making them ideal for industrial floors and surfaces exposed to harsh chemicals. Polyurethane coatings, on the other hand, offer superior flexibility, abrasion resistance, and UV stability, making them suitable for surfaces that require impact resistance and outdoor applications.
In essence, the choice between epoxy and polyurethane depends on the specific requirements of your application, such as exposure conditions and desired finish.
How do environmental factors affect coating performance?
Environmental factors, such as temperature, humidity, and exposure to chemicals, can significantly impact the performance of industrial coatings. High humidity levels can affect the curing process, leading to poor adhesion and reduced durability. Similarly, extreme temperatures can cause coatings to crack or become brittle. For more insights on coating durability, explore how architectural paints enhance durability.
Therefore, it’s essential to consider these factors when selecting and applying industrial coatings to ensure they provide the desired protection and longevity.
What are the best practices for maintaining industrial coatings?
To maintain industrial coatings effectively, regular inspections and cleaning are crucial. Look for signs of wear, such as cracks, peeling, or discoloration, and address them promptly to prevent further damage. Use appropriate cleaning agents that do not degrade the coating material.
Moreover, follow the manufacturer’s guidelines for maintenance and reapplication schedules to ensure the coatings continue to perform optimally.
Are there eco-friendly options available for industrial coatings?
Yes, eco-friendly industrial coatings are available and gaining popularity. These coatings typically have low or no volatile organic compounds (VOCs), reducing their environmental impact. Powder coatings are an excellent example of an eco-friendly option, as they contain no solvents and produce minimal waste.
How often should industrial coatings be inspected and reapplied?
The frequency of inspections and reapplication depends on the specific coating type, application environment, and wear conditions. Generally, annual inspections are recommended to identify any issues early. Reapplication schedules can vary, with some coatings lasting several years before needing touch-ups or full reapplication. For more detailed information on protective coating technologies, you can explore modern industrial structures.
By following these guidelines, you can ensure that your industrial coatings continue to provide effective protection and enhance the efficiency of your operations.