Top Marine Coating Solutions for Long-Lasting Industrial Performance
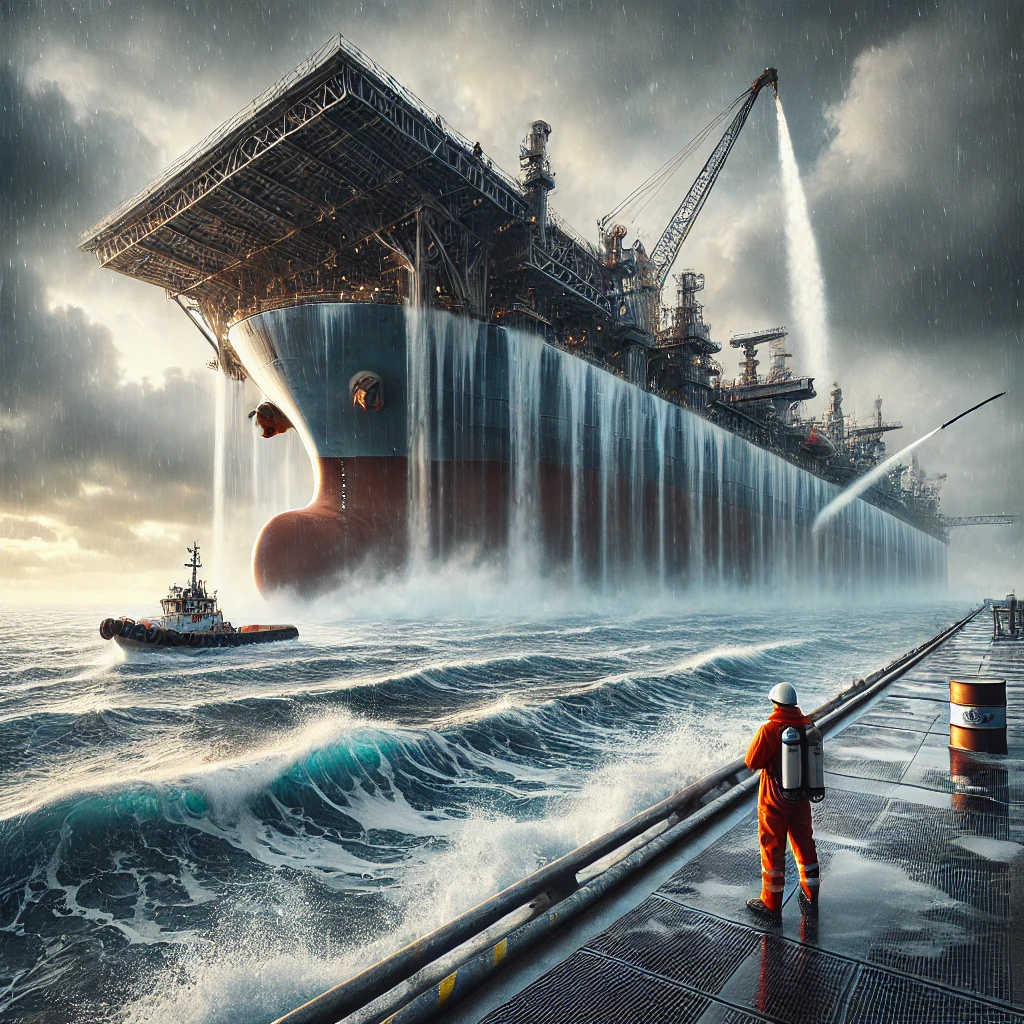
Article-at-a-Glance
- Marine coatings protect vessels from harsh sea conditions, reducing corrosion and wear.
- These coatings extend the lifespan of marine vessels, saving costs on repairs and replacements.
- Different types of coatings, such as epoxy, polyurethane, and antifouling, serve various protective purposes.
- Choosing the right marine coating involves considering environmental conditions, compatibility, and regulatory standards.
- Successful case studies demonstrate the effectiveness of marine coatings in real-world applications.
Top Marine Coating Solutions for Long-Lasting Industrial Performance
Importance of Marine Coatings for Industrial Performance
Marine coatings are essential for protecting vessels and offshore structures from the harsh marine environment. These coatings act as a barrier against corrosion, wear, and fouling, ensuring that vessels remain operational and efficient. Without proper coating, the structural integrity of marine vessels can quickly deteriorate, leading to costly repairs and downtime.
Protecting Against Corrosion and Wear
Corrosion is one of the biggest challenges faced by marine vessels. Saltwater, humidity, and varying temperatures can cause metal surfaces to corrode rapidly. Marine coatings provide a protective layer that prevents direct contact between the metal surface and the corrosive elements.
Besides corrosion, marine coatings also protect against wear and tear caused by mechanical impacts and abrasive forces. This is particularly important for areas like cargo holds and ballast tanks, which are frequently exposed to harsh conditions.
Extending the Lifespan of Marine Vessels
Marine coatings significantly extend the lifespan of vessels by providing long-lasting protection. This means that ships can remain in service for longer periods without needing extensive repairs or replacements. In turn, this leads to reduced operational costs and increased profitability for shipping companies. For more information on marine coatings, visit PPG’s marine solutions.
For example, a well-coated cargo ship can operate efficiently for decades, whereas an uncoated or poorly coated ship might need frequent maintenance and face early decommissioning.
Cost-Effective Maintenance Solutions
Investing in high-quality marine coatings is a cost-effective solution for maintaining vessels. While the initial cost of applying these coatings might be high, the long-term savings on maintenance and repairs make it worthwhile.
Regular maintenance of coatings, such as touch-ups and reapplications, ensures that the protective layer remains intact and continues to provide optimal protection. This proactive approach to maintenance helps avoid unexpected costs and operational disruptions.
Key Benefits of Marine Coatings
Increase Durability and Reliability
Marine coatings enhance the durability and reliability of vessels. By providing a robust protective layer, these coatings ensure that vessels can withstand the challenging conditions of the marine environment. This increased durability translates to fewer breakdowns and higher operational efficiency.
Enhance Efficiency and Performance
Well-applied marine coatings reduce drag and improve the hydrodynamic performance of vessels. This means that ships can move more smoothly through the water, leading to fuel savings and reduced emissions. Additionally, coatings that prevent fouling, such as barnacle growth, help maintain the vessel’s speed and efficiency over time.
Environmental Protection and Compliance
Modern marine coatings are designed to be environmentally friendly and comply with stringent regulations. These coatings minimize the release of harmful substances into the ocean, protecting marine life and ecosystems. Furthermore, using eco-friendly coatings helps shipping companies meet regulatory requirements and avoid penalties.
Types of Marine Coatings
Epoxy Coatings
Epoxy coatings are widely used in the marine industry due to their excellent adhesion and durability. These coatings provide a strong barrier against water and chemicals, making them ideal for areas exposed to harsh conditions, such as ballast tanks and cargo holds. For more information on high-performance coatings, visit PPG High-Performance Coatings.
However, epoxy coatings can be sensitive to UV exposure, which can cause them to yellow or chalk over time. Therefore, they are often used in combination with a topcoat, such as polyurethane, to enhance their longevity.
Polyurethane Coatings
Polyurethane coatings offer superior resistance to weathering, abrasion, and impact. These coatings are commonly used on exterior surfaces, where they provide long-term protection against the elements. Their excellent color and gloss retention make them a popular choice for aesthetic applications as well.
Antifouling Coatings
Antifouling coatings are designed to prevent the growth of marine organisms, such as barnacles and algae, on the hull of a vessel. These coatings contain biocides that deter fouling organisms, keeping the hull clean and maintaining the vessel’s performance.
Using antifouling coatings reduces the need for frequent cleaning and maintenance, saving time and resources. It also helps improve fuel efficiency by reducing drag caused by fouling.
Polyurethane coatings are known for their flexibility and toughness. They are highly resistant to weathering, abrasion, and impact, making them suitable for exterior surfaces exposed to harsh marine environments. The superior color and gloss retention of polyurethane coatings also make them a preferred choice for aesthetic applications on vessels.
Antifouling Coatings
Antifouling coatings play a crucial role in maintaining the efficiency and performance of marine vessels. These coatings are formulated to prevent the growth of marine organisms such as barnacles, algae, and mussels on the hull. Fouling can significantly increase drag, reducing the vessel’s speed and fuel efficiency. By using antifouling coatings, vessels can maintain a smoother hull surface, leading to better performance and lower fuel consumption. For more information, you can visit PPG’s marine coatings page.
There are different types of antifouling coatings, including hard antifouling, ablative antifouling, and foul-release coatings. Each type has its specific application and benefits, depending on the vessel’s operational profile and maintenance schedule. For more information on protective coatings, you can read about protective coatings for extreme environments.
Non-Skid Coatings
Non-skid coatings are essential for ensuring the safety of crew members on deck. These coatings provide a rough, textured surface that reduces the risk of slips and falls, especially in wet conditions. Non-skid coatings are commonly applied to walkways, ramps, and other areas where foot traffic is high.
Besides safety, non-skid coatings also offer excellent durability and resistance to chemicals, oils, and abrasion. This makes them suitable for various marine applications, including offshore platforms and industrial vessels.
Factors to Consider When Choosing Marine Coatings
Choosing the right marine coating for your vessel involves considering several factors. These factors ensure that the coating provides optimal protection and performance in the specific conditions your vessel will encounter.
Environmental Conditions and Exposure
The environmental conditions and exposure levels your vessel will face play a significant role in determining the appropriate marine coating. Factors such as temperature, humidity, salinity, and UV exposure can affect the performance and longevity of the coating.
For example, vessels operating in tropical regions with high UV exposure might require coatings with enhanced UV resistance. Similarly, vessels in colder climates may need coatings that can withstand freezing temperatures and ice abrasion.
Compatibility with Vessel Materials
It’s essential to choose a marine coating that is compatible with the materials used in your vessel’s construction. Different materials, such as steel, aluminium, and fiberglass, have varying requirements for surface preparation and coating adhesion.
Using a coating that is not compatible with the vessel’s material can lead to poor adhesion, reduced protection, and premature failure. Therefore, it’s crucial to consult with coating manufacturers and experts to ensure compatibility and optimal performance.
Application Methods and Ease of Use
The application method and ease of use of marine coatings are also important considerations. Some coatings require specialized equipment and expertise for application, while others can be applied using standard methods.
For example, spray-applied coatings might provide a more uniform finish but require skilled operators and proper equipment. On the other hand, brush or roller-applied coatings might be more straightforward but could result in a less uniform finish.
Regulatory Requirements and Standards
Marine coatings must comply with various regulatory requirements and standards to ensure safety and environmental protection. These regulations can vary depending on the vessel’s operating region and the type of cargo it carries.
It’s essential to stay informed about the latest regulations and choose coatings that meet or exceed these standards. Compliance not only ensures the safety of the vessel and crew but also helps avoid potential fines and legal issues.
Coating Type | Key Features | Best For | Performance |
---|---|---|---|
PPG SIGMAGLIDE® 2390 | Biocide-free, silicone-based fouling release | Large commercial vessels | Up to 20% power savings, <1% speed loss |
PPG NEXEON™ 810 | Ultra low-friction, copper-free antifouling | Vessels with idle periods | Up to 25% emissions reduction, 60 days idle resistance |
PPG SIGMA SAILADVANCE™ NX | Advanced antifouling technology | Wide range of vessels | Reduced energy use, lower operational costs |
PPG PHENGUARD® 985 | Premium phenolic epoxy tanklining | Chemical/product tankers | High chemical and temperature resistance |
PPG SIGMACOVER™ 380 | Universal anticorrosive epoxy primer | Water ballast tanks | Year-round application, PSPC-approved |
PPG SIGMASHIELD™ 1200 | Reinforced abrasion/impact resistant | Ice-going vessels | Independently tested for ice service |
Pulsed Eddy Current (PEC) Coatings | Advanced non-destructive testing | Superyachts, high-value vessels | Allows inspection without coating removal |
Antifouling Coatings
Antifouling coatings play a crucial role in maintaining the efficiency and performance of marine vessels. These coatings are formulated to prevent the growth of marine organisms such as barnacles, algae, and mussels on the hull. Fouling can significantly increase drag, reducing the vessel’s speed and fuel efficiency. By using antifouling coatings, vessels can maintain a smoother hull surface, leading to better performance and lower fuel consumption.
There are different types of antifouling coatings, including hard antifouling, ablative antifouling, and foul-release coatings. Each type has its specific application and benefits, depending on the vessel’s operational profile and maintenance schedule. For instance, weather-resistant paints can significantly enhance the durability of coatings exposed to harsh marine environments.
Non-Skid Coatings
Non-skid coatings are essential for ensuring the safety of crew members on deck. These coatings provide a rough, textured surface that reduces the risk of slips and falls, especially in wet conditions. Non-skid coatings are commonly applied to walkways, ramps, and other areas where foot traffic is high.
Besides safety, non-skid coatings also offer excellent durability and resistance to chemicals, oils, and abrasion. This makes them suitable for various marine applications, including offshore platforms and industrial vessels. Learn more about the high-performance acrylic for industrial surfaces used in these coatings.
Case Studies of Successful Marine Coating Applications
Large Container Vessels
Large container vessels face unique challenges due to their size and operational demands. One notable case study involves a major shipping company that applied advanced antifouling coatings to its fleet of container ships. The result was a significant reduction in fuel consumption and maintenance costs, leading to improved operational efficiency and profitability.
Offshore Platforms
Offshore platforms are exposed to some of the harshest marine conditions, including saltwater, high winds, and extreme temperatures. A leading oil company implemented a comprehensive coating system for its offshore platforms, using a combination of epoxy and polyurethane coatings. This approach provided long-lasting protection against corrosion and wear, ensuring the platforms’ structural integrity and safety.
Inland Waterway Vessels
Inland waterway vessels, such as barges and towboats, operate in freshwater environments but still face challenges like abrasion and impact. A successful case study involves a barge operator who used non-skid coatings on the deck and epoxy coatings in the cargo hold. This combination enhanced safety for the crew and provided robust protection against the abrasive materials transported by the barge.
Factors to Consider When Choosing Marine Coatings
Choosing the right marine coating for your vessel involves considering several factors. These factors ensure that the coating provides optimal protection and performance in the specific conditions your vessel will encounter.
Environmental Conditions and Exposure
The environmental conditions and exposure levels your vessel will face play a significant role in determining the appropriate marine coating. Factors such as temperature, humidity, salinity, and UV exposure can affect the performance and longevity of the coating.
For example, vessels operating in tropical regions with high UV exposure might require coatings with enhanced UV resistance. Similarly, vessels in colder climates may need coatings that can withstand freezing temperatures and ice abrasion.
Compatibility with Vessel Materials
It’s essential to choose a marine coating that is compatible with the materials used in your vessel’s construction. Different materials, such as steel, aluminium, and fiberglass, have varying requirements for surface preparation and coating adhesion.
Using a coating that is not compatible with the vessel’s material can lead to poor adhesion, reduced protection, and premature failure. Therefore, it’s crucial to consult with coating manufacturers and experts to ensure compatibility and optimal performance. For example, understanding the industrial paint application tips can help in selecting the right coating.
Application Methods and Ease of Use
The application method and ease of use of marine coatings are also important considerations. Some coatings require specialized equipment and expertise for application, while others can be applied using standard methods.
For example, spray-applied coatings might provide a more uniform finish but require skilled operators and proper equipment. On the other hand, brush or roller-applied coatings might be more straightforward but could result in a less uniform finish. For more details, check out this guide on industrial paint application tips.
Regulatory Requirements and Standards
Marine coatings must comply with various regulatory requirements and standards to ensure safety and environmental protection. These regulations can vary depending on the vessel’s operating region and the type of cargo it carries. For more information on high-performance coatings, visit PPG’s high-performance coatings resource page.
It’s essential to stay informed about the latest regulations and choose coatings that meet or exceed these standards. Compliance not only ensures the safety of the vessel and crew but also helps avoid potential fines and legal issues.
Case Studies of Successful Marine Coating Applications
Large Container Vessels
Large container vessels face unique challenges due to their size and operational demands. One notable case study involves a major shipping company that applied advanced antifouling coatings to its fleet of container ships. The result was a significant reduction in fuel consumption and maintenance costs, leading to improved operational efficiency and profitability.
Offshore Platforms
Offshore platforms are exposed to some of the harshest marine conditions, including saltwater, high winds, and extreme temperatures. A leading oil company implemented a comprehensive coating system for its offshore platforms, using a combination of epoxy and polyurethane coatings. This approach provided long-lasting protection against corrosion and wear, ensuring the platforms’ structural integrity and safety.
Inland Waterway Vessels
Inland waterway vessels, such as barges and towboats, operate in freshwater environments but still face challenges like abrasion and impact. A successful case study involves a barge operator who used non-skid coatings on the deck and epoxy coatings in the cargo hold. This combination enhanced safety for the crew and provided robust protection against the abrasive materials transported by the barge.
Conclusion: Making the Right Choice for Long-Lasting Performance
Choosing the right marine coating solution is crucial for ensuring the long-lasting performance and protection of your vessel. By considering factors such as environmental conditions, material compatibility, application methods, and regulatory requirements, you can select the best coating for your needs.
Investing in high-quality marine coatings not only extends the lifespan of your vessel but also enhances its efficiency, safety, and compliance with environmental standards. Whether you operate large container ships, offshore platforms, or inland waterway vessels, the right coating solution can make a significant difference in your operational success.
IPS Paint Supplies
Frequently Asked Questions (FAQ)
1. What are marine coatings, and why are they important?
Marine coatings are protective layers applied to the surfaces of ships, offshore structures, and other marine environments. They are crucial for preventing corrosion, fouling, and wear, thereby extending the lifespan of marine assets and maintaining their structural integrity.
2. What types of marine coatings are available for industrial use?
There are several types of marine coatings, including:
- Anti-corrosion coatings: Protect metal surfaces from rust and degradation.
- Anti-fouling coatings: Prevent marine organisms like barnacles from attaching to submerged surfaces.
- Epoxy coatings: Provide a durable and resistant layer, ideal for high-impact areas.
- Polyurethane coatings: Offer flexibility and resistance to UV radiation and weathering.
- Silicone-based coatings: Often used for fouling release, allowing easier cleaning of surfaces.
3. How do I choose the right marine coating for my application?
Choosing the right marine coating depends on several factors, including:
- Environmental conditions: Saltwater, temperature, and humidity levels.
- Material of the substrate: Whether the surface is metal, fiberglass, or another material.
- Desired lifespan: How long the coating needs to last before reapplication.
- Regulatory requirements: Compliance with environmental and safety standards.
4. What are the benefits of using anti-fouling coatings?
Anti-fouling coatings prevent the growth of marine organisms on submerged surfaces. This not only improves fuel efficiency by reducing drag but also minimizes the risk of damage and corrosion. Additionally, it helps in maintaining the vessel’s speed and performance over time.
5. How often should marine coatings be reapplied?
The reapplication frequency depends on the type of coating, environmental exposure, and the performance of the existing layer. Typically, high-quality marine coatings can last between 3 to 10 years, but regular inspections are recommended to determine when reapplication is necessary.
6. What environmental regulations should I be aware of when selecting marine coatings?
Environmental regulations vary by region and can include restrictions on certain chemicals, such as organotin compounds used in anti-fouling paints. It’s essential to choose coatings that comply with local and international regulations like the IMO (International Maritime Organization) guidelines.
7. Can marine coatings be applied in cold weather or high humidity?
Some marine coatings are formulated for application in specific weather conditions. For instance, epoxy coatings may require certain temperature and humidity levels to cure properly. It’s important to follow the manufacturer’s guidelines for optimal results in different environmental conditions.
8. How do I prepare a surface for marine coating application?
Surface preparation is critical for the adhesion and effectiveness of marine coatings. Steps typically include:
- Cleaning: Removing salt, dirt, and oil from the surface.
- Surface roughening: Sandblasting or abrading to create a profile for better adhesion.
- Priming: Applying a primer that is compatible with both the substrate and the topcoat.
9. What are the latest advancements in marine coating technology?
Recent advancements in marine coatings include:
- Self-healing coatings: These coatings can repair minor scratches and damages automatically, extending their lifespan.
- Biocide-free anti-fouling coatings: Environmentally friendly options that prevent fouling without releasing harmful chemicals.
- Nanotechnology-enhanced coatings: Provide superior durability and resistance to corrosion and fouling.
10. Can marine coatings help in energy savings?
Yes, certain marine coatings, especially anti-fouling and smooth-finish coatings, can reduce friction and drag, leading to improved fuel efficiency and lower energy consumption. This can result in significant cost savings over time.