How to Choose the Right Marine Coatings for Industrial Structures
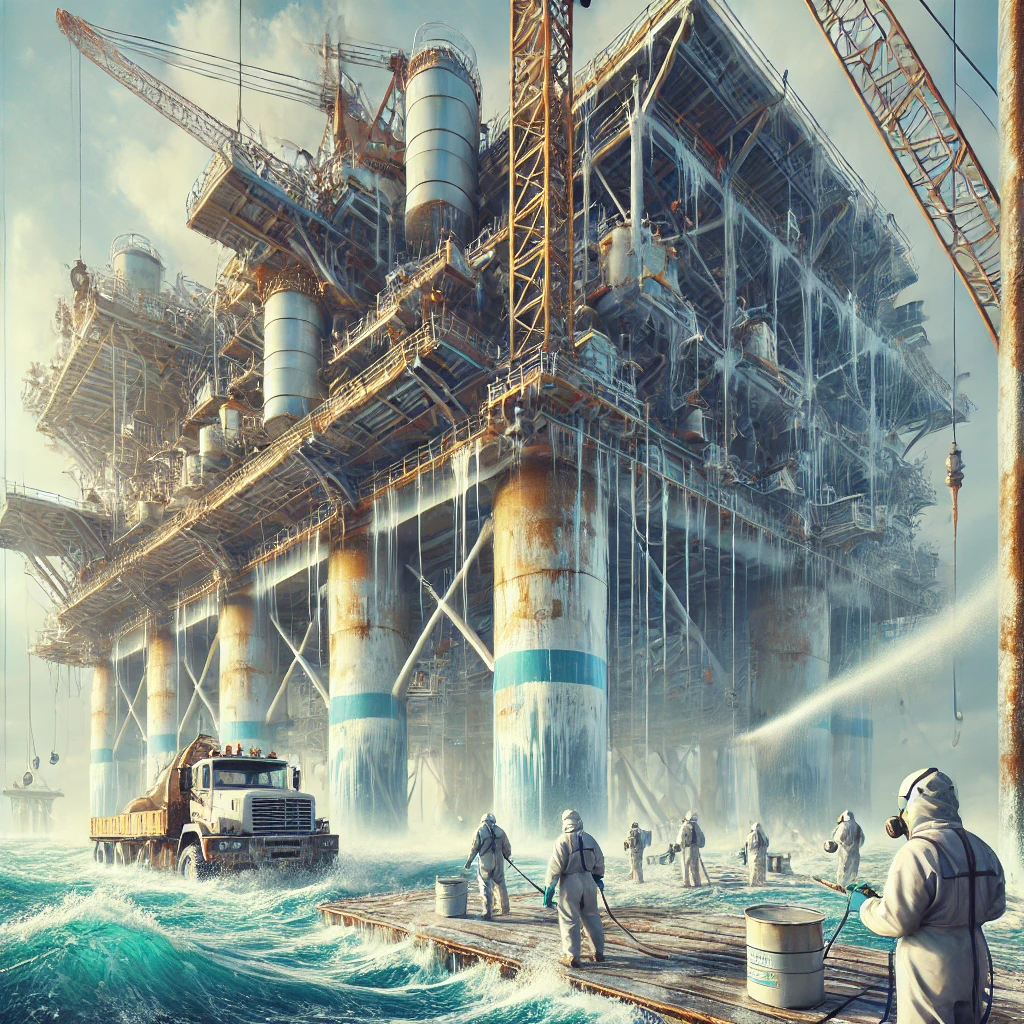
Key Takeaways
- Marine coatings are essential for protecting industrial structures from harsh marine environments.
- Consider environmental regulations and specific substrate materials when choosing a coating.
- Different types of marine coatings, such as epoxy and polyurethane, offer unique benefits.
- Application methods like spray, electrostatic, and powder coating are crucial for effective results.
- Balancing cost and performance is key to making the right choice for your specific needs.
How to Choose the Right Marine Coatings for Industrial Structures
Choosing the right marine coatings for industrial structures is crucial. These coatings protect against corrosion, weather, and other environmental factors. A well-chosen coating can extend the life of a structure, reduce maintenance costs, and ensure safety.
Before diving into the specifics, let’s understand why marine coatings are so important. Industrial structures, such as ships, offshore platforms, and storage facilities, are constantly exposed to harsh marine environments. Saltwater, humidity, and varying temperatures can cause significant damage over time.
Importance of Marine Coatings for Industrial Structures
Marine coatings provide a protective barrier against these harsh conditions. They prevent corrosion, which is the primary enemy of metal structures in marine environments. By doing so, they help maintain the structural integrity and appearance of these assets.
“Marine coatings are waterproof, protective layers applied to surfaces exposed to or immersed in fresh, brackish, and/or salt water.”
Besides that, marine coatings also play a crucial role in reducing maintenance costs. Regular maintenance and repairs can be expensive and time-consuming. By using the right coatings, you can minimize the need for frequent touch-ups and repairs.
Factors to Consider When Choosing Marine Coatings
Choosing the right marine coating involves several factors. Each factor plays a role in ensuring the coating performs effectively and lasts long. Here are the key considerations: enhance outdoor durability with weather-resistant paints.
- Environmental and Regulatory Requirements
- Durability and Longevity
- Application Methods
- Cost Considerations
- Compatibility with Substrates
Environmental and Regulatory Requirements
First and foremost, you need to consider environmental and regulatory requirements. Different regions have varying regulations regarding the use of certain chemicals and materials in marine coatings. Ensure the coating you choose complies with these regulations to avoid legal issues.
Durability and Longevity
Durability and longevity are critical factors. You want a coating that can withstand the harsh marine environment for an extended period. Look for coatings that offer excellent resistance to corrosion, UV rays, and mechanical wear. The longer the coating lasts, the less frequently you’ll need to reapply it, saving both time and money.
For example, epoxy coatings are known for their durability and excellent adhesion properties. They form a hard, protective layer that can withstand the rigors of marine environments.
Application Methods
Application methods also play a significant role in the effectiveness of marine coatings. Different coatings require different application techniques to achieve the best results. Common methods include:
- Spray Application
- Electrostatic and Electrocoating
- Powder Coating
- Roller and Brush Application
Choosing the right application method depends on the type of coating and the surface you’re working with. For instance, spray application is ideal for large, flat surfaces, while brush application works well for smaller, intricate areas.
Cost Considerations
Cost is always a significant factor in choosing marine coatings. While it might be tempting to go for the cheapest option, it’s essential to consider the long-term benefits and costs. Cheaper coatings might require more frequent applications and repairs, leading to higher costs over time.
Investing in high-quality coatings can save money in the long run by reducing maintenance and extending the life of your structures. Therefore, balance the initial cost with the long-term benefits to make an informed decision.
Compatibility with Substrates
The compatibility of the coating with the substrate material is another crucial factor. Different coatings are designed to work with specific materials such as steel, aluminium, or concrete. Using an incompatible coating can lead to poor adhesion and reduced effectiveness. For more information, explore the protective coatings for extreme environments.
For instance, epoxy coatings work well with steel and aluminium, providing excellent adhesion and durability. On the other hand, polyurethane coatings are versatile and can be used on various substrates, including wood and fiberglass.
Types of Marine Coatings
There are several types of marine coatings, each with unique properties and benefits. Understanding these types can help you choose the best one for your specific needs. For instance, you might want to explore the benefits of intumescent paints for fire resistance.
Epoxy Coatings
Epoxy coatings are known for their excellent adhesion and durability. They form a hard, protective layer that can withstand harsh marine environments. Epoxy coatings are ideal for steel and aluminium surfaces, providing long-lasting protection against corrosion.
Additionally, epoxy coatings have excellent resistance to chemicals and solvents, making them suitable for industrial structures exposed to harsh chemicals.
Polyurethane Coatings
Polyurethane coatings are versatile and offer a range of benefits. They provide excellent UV resistance, making them ideal for structures exposed to sunlight. Polyurethane coatings also offer good flexibility, allowing them to expand and contract with temperature changes without cracking. Learn more about enhancing outdoor durability with weather-resistant paints.
These coatings are suitable for various substrates, including wood, fiberglass, and metals. They also provide a glossy finish, enhancing the appearance of the coated surface.
Anti-fouling Coatings
Anti-fouling coatings are specifically designed to prevent the growth of marine organisms on submerged surfaces. These coatings release biocides that deter organisms like barnacles and algae from attaching to the surface.
Using anti-fouling coatings can improve the efficiency of ships and other marine structures by reducing drag and preventing the buildup of marine growth. This, in turn, can lead to fuel savings and reduced maintenance costs.
Inorganic Zinc Coatings
Inorganic zinc coatings offer excellent corrosion resistance, making them ideal for protecting steel structures in marine environments. These coatings contain a high percentage of zinc, which provides a sacrificial layer that corrodes instead of the underlying metal. For more information on protective coatings, you can explore protective coatings for extreme environments.
Inorganic zinc coatings are often used as primers, providing a strong base for other coatings to adhere to. They are commonly used in combination with epoxy or polyurethane topcoats for enhanced protection.
Sealants and Primers
Sealants and primers play a crucial role in the coating process. Primers are applied to the substrate before the topcoat, ensuring better adhesion and providing an additional layer of protection. Sealants, on the other hand, are used to fill gaps and cracks, preventing moisture and contaminants from penetrating the surface.
Using the right sealants and primers can significantly enhance the performance and longevity of the marine coating system.
Application Techniques for Marine Coatings
Applying marine coatings correctly is as important as choosing the right type. Different application techniques can affect the coating’s performance and durability.
Spray Application
Spray application is a common method for applying marine coatings, especially on large, flat surfaces. This technique allows for even coverage and a smooth finish. It is also efficient, reducing the time required for application.
However, spray application requires specialized equipment and trained personnel to ensure proper application and avoid issues like overspray and uneven coating thickness.
Electrostatic and Electrocoating
Electrostatic and electrocoating techniques involve applying an electrical charge to the coating material, which is then attracted to the oppositely charged surface. This method ensures even coverage and excellent adhesion, making it ideal for complex shapes and hard-to-reach areas.
Electrocoating is commonly used for applying primers and base coats, providing a strong foundation for subsequent layers.
Powder Coating
Powder coating involves applying a dry powder to the surface, which is then cured under heat to form a hard, protective layer. This technique offers excellent durability and resistance to corrosion and chemicals. Learn more about different marine coatings for various applications.
Powder coating is suitable for various substrates, including metals and plastics. It also provides a uniform finish and is environmentally friendly, as it produces minimal waste.
Roller and Brush Application
Roller and brush application methods are suitable for smaller areas and intricate surfaces. These techniques allow for precise application and control, making them ideal for touch-ups and detailed work.
While they may be slower than spray application, roller and brush methods ensure thorough coverage and are less likely to result in overspray and waste.
Factor | Consideration | Recommended Coating Type |
---|---|---|
Corrosion Protection | Exposure to saltwater environments | Epoxy-based coatings (e.g., Transpoxy ZP Primer 1.61) |
Chemical Resistance | Contact with fuels, solvents, or cleaning agents | Vinyl ester coatings or polysiloxane technologies |
Impact and Abrasion Resistance | High-traffic areas or potential for physical damage | Epoxy-based coatings (e.g., Transpoxy Barrier 2.18) |
Antifouling Properties | Submerged structures or areas prone to marine growth | Specialized antifouling coatings |
UV Resistance | Surfaces exposed to intense sunlight | Polyurethane-based coatings (e.g., Transurethane Finish HB 3.44) |
Environmental Conditions | Extreme weather, temperature fluctuations | Weather-resistant industrial paints |
Substrate Material | Steel, concrete, aluminum, or wood | Material-specific coatings (e.g., epoxy for steel, specialized coatings for aluminium) |
Intended Use | Food processing, high-temperature environments, waterproofing | FDA-compliant, high-temperature, or waterproof coatings |
Environmental Compliance | Eco-friendly requirements | Low-VOC or environmentally friendly coatings |
Application Method | Ease of application and maintenance | Coatings suitable for brush, spray, or roller application |
Case Studies of Effective Marine Coating Use
Real-world examples can provide valuable insights into the effectiveness of different marine coatings. Here are a few case studies that highlight successful applications:
Commercial Shipping Vessels
Commercial shipping vessels face constant exposure to harsh marine environments. A leading shipping company decided to use epoxy coatings for their fleet’s hulls. The result was a significant reduction in corrosion and maintenance costs. The epoxy coatings provided excellent adhesion and durability, protecting the vessels from the rigors of the sea.
“Using epoxy coatings for our fleet’s hulls has reduced our maintenance costs by 30% and extended the lifespan of our vessels.”
Oil Rigs and Offshore Platforms
Oil rigs and offshore platforms are subjected to extreme conditions, including saltwater, UV exposure, and mechanical wear. A major oil company opted for a combination of inorganic zinc primers and polyurethane topcoats for their offshore structures. This coating system provided robust protection against corrosion and weathering, ensuring the longevity and safety of the platforms.
“The combination of inorganic zinc primers and polyurethane topcoats has significantly improved the durability and safety of our offshore platforms.”
By choosing the right marine coatings and application techniques, these companies were able to enhance the performance and longevity of their industrial structures, demonstrating the importance of making informed decisions in this critical area.
Case Studies of Effective Marine Coating Use
Real-world examples can provide valuable insights into the effectiveness of different marine coatings. Here are a few case studies that highlight successful applications:
Commercial Shipping Vessels
Commercial shipping vessels face constant exposure to harsh marine environments. A leading shipping company decided to use epoxy coatings for their fleet’s hulls. The result was a significant reduction in corrosion and maintenance costs. The epoxy coatings provided excellent adhesion and durability, protecting the vessels from the rigors of the sea.
“Using epoxy coatings for our fleet’s hulls has reduced our maintenance costs by 30% and extended the lifespan of our vessels.”
Oil Rigs and Offshore Platforms
Oil rigs and offshore platforms are subjected to extreme conditions, including saltwater, UV exposure, and mechanical wear. A major oil company opted for a combination of inorganic zinc primers and polyurethane topcoats for their offshore structures. This coating system provided robust protection against corrosion and weathering, ensuring the longevity and safety of the platforms.
“The combination of inorganic zinc primers and polyurethane topcoats has significantly improved the durability and safety of our offshore platforms.”
Pipeline and Storage Facilities
Pipelines and storage facilities also require robust protection against corrosion and environmental factors. A pipeline company chose to use anti-fouling coatings to prevent the build up of marine organisms and improve the efficiency of their pipelines. This decision led to reduced maintenance and operational costs, as well as improved flow rates.
“Implementing anti-fouling coatings on our pipelines has not only reduced maintenance costs but also improved the overall efficiency of our operations.”
Final Thoughts: Making the Right Choice
Choosing the right marine coating for your industrial structures is a critical decision that can impact the longevity, safety, and maintenance costs of your assets. By considering factors such as environmental regulations, durability, application methods, cost, and substrate compatibility, you can make an informed choice that meets your specific needs.
Balancing Cost and Performance
Balancing cost and performance is key. While it might be tempting to opt for the cheapest coating, investing in high-quality coatings can save you money in the long run by reducing maintenance and extending the life of your structures. Evaluate the long-term benefits and costs to make an informed decision.
Consulting with Experts
Consulting with experts can provide valuable insights and recommendations. Coating manufacturers and industry professionals can help you choose the best coating for your specific needs and ensure proper application techniques are used. Their expertise can help you avoid common pitfalls and achieve the best results.
IPS Paint Supplies
Protect your marine investments with our specialised coatings and paints, meticulously crafted to endure the rigorous demands of the marine industry. At IPS Paint Supplies, we provide a comprehensive range of marine coatings, including top brands like PPG Sigma, Jotun, and Hempel, ensuring superior protection and durability in even the harshest marine environments. Whether you’re safeguarding vessels, offshore structures, or coastal installations, our high-performance coatings are designed to withstand the toughest conditions.
Our marine coatings are engineered to resist the corrosive impact of saltwater, UV exposure, and relentless environmental challenges. Leveraging advanced technology, these coatings deliver exceptional adhesion and long-lasting protection, helping to minimize maintenance costs and prolong the lifespan of your assets. Available in a variety of finishes and colors, our products not only protect but also enhance the visual appeal and operational efficiency of your marine structures.
Serving industries such as shipping, offshore oil and gas, and coastal infrastructure, our marine coatings adhere to stringent international standards and are trusted by professionals around the globe. At IPS Paint Supplies, we collaborate with leading brands to offer coatings that combine performance with reliability. Our knowledgeable team is ready to help you choose the ideal products tailored to your specific marine requirements.
Frequently Asked Questions (FAQ)
Here are some frequently asked questions about marine coatings for industrial structures:
What are the most durable marine coatings for industrial use?
Epoxy coatings are known for their durability and excellent adhesion properties. They form a hard, protective layer that can withstand the rigors of marine environments. Inorganic zinc coatings also offer excellent corrosion resistance and are often used as primers for additional protection.
How do anti-fouling coatings work?
Anti-fouling coatings release biocides that deter marine organisms like barnacles and algae from attaching to the surface. This prevents the buildup of marine growth, reducing drag and improving the efficiency of ships and other marine structures. Anti-fouling coatings are essential for maintaining the performance and longevity of submerged surfaces.
What regulations should I be aware of when applying marine coatings?
Different regions have varying regulations regarding the use of certain chemicals and materials in marine coatings. It’s essential to ensure that the coating you choose complies with these regulations to avoid legal issues. Consulting with experts and coating manufacturers can help you navigate these requirements and make informed decisions.